Keycode as an Buildlink Asset Management solution
Buildlink Ltd. as an key strategic partner of Keycotek, operates essential infrastructure involving numerous electricity measurement center devices.
In future as their operations scales, they have growing challenges in efficiently tracking, maintaining, and managing these vital assets.
Buildlink's current asset management system handles internal IoT data like electricity measurements, device diagnostics and calibration.
Modern Keycotek's asset management service offers a comprehensive solution that complements and enhances Buildlink's existing capabilities.
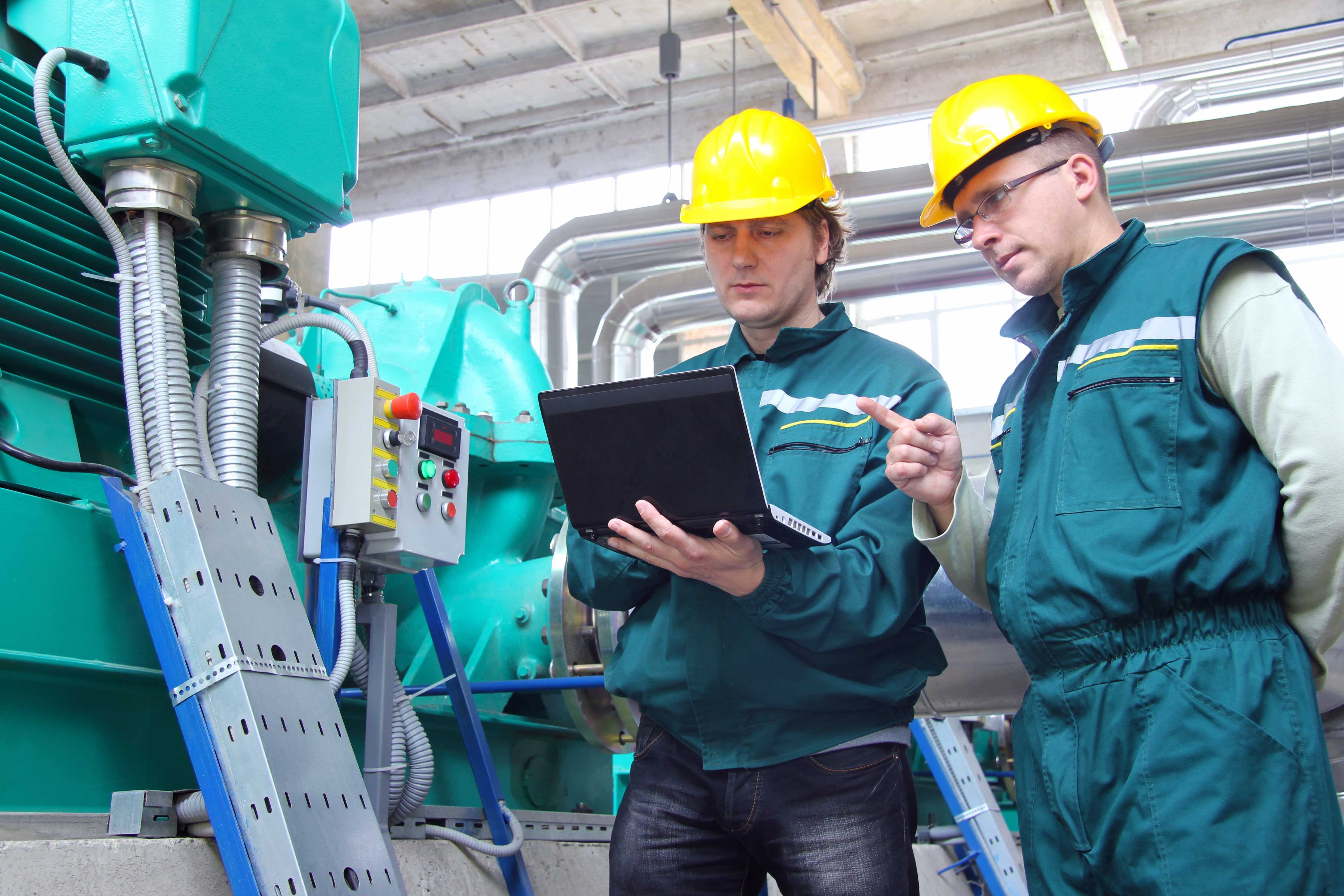
Requirements and solution
Recognizing the need for a more robust solution, Buildlink Ltd. conducted an in-depth analysis of their Asset Management requirements specifically for this equipment. This process resulted in a clear mandate for a system possessing the following key capabilities:
Workflow: Intuitive, flexible, and easily configurable workflows.
Compliance: Built-in support for relevant industry standards, such as the ISO 50000 series.
Digital Integration: Capabilities to support Digital Twins, Digital Product Passports, and IoT data integration.
Physical Identification: Ready-to-use QR code and NFC tags/labels for seamless asset identification in the field.
Data Management: Ability to define custom metadata fields alongside managing both common and unique device information.
Resource Linking: Centralized management for associated digital resources like manuals, documentation, and external links.
User Control: Sophisticated user management featuring role-based access control tied into operational workflows.
Logging & Feedback: Comprehensive logs for maintenance activities and user interactions, including mechanisms for feedback capture.
This detailed list formed the foundation for their search for a next-generation Asset Management platform.
Use case: Streamlining Product Information Sharing with QR Codes
Problem: Ensuring local partners have immediate access to the most up-to-date and relevant product specifications, instructions, work safety guidelines, and other digital resources can be challenging. Traditional methods like email, shared drives, or physical documentation often lead to version control issues, delays in information dissemination, and potential for errors.
Solution: The company’s product manager utilizes a system to associate common or unique QR codes with specific devices or product lines. These QR codes, when scanned by local partners using their smartphones or tablets, directly link to a centralized digital repository containing all necessary information.
Scenario/workflow:
Product Manager Updates Resources: The product manager updates a product specification document, adds a new troubleshooting guide, or revises safety protocols within the central digital repository.
QR Code Association: The product manager ensures the relevant QR code for the specific device or product line is linked to these updated digital resources. This association is managed within a user-friendly platform.
Deployment: QR codes are physically affixed to the devices, included in manufacturing or provided to local partners.
Local Partner Access: A technician at a measurement center in Helsinki needs to assemble a new device. They scan the QR code on the device using a dedicated mobile application or a standard QR code reader.
Instant Information Retrieval: The scan instantly directs the technician to the latest version of the assembly instructions, technical specifications, and any relevant safety guidelines in their preferred language (if the system supports multilingual access).
Maintenance and Troubleshooting: Later, a maintenance engineer in Tampere needs to troubleshoot an issue. They scan the QR code on the device and gain immediate access to maintenance manuals, diagnostic procedures, and frequently asked questions.
Usage Guidelines: A new user in Finland scans the QR code to access user manuals, quick start guides, and best practices for operating the device effectively and safely.
Benefits:
- Real-time Information Access: Local partners always have access to the most current information, eliminating the risk of using outdated documents.
- Improved Efficiency: Faster access to information reduces delays in assembly, maintenance, and troubleshooting.
- Enhanced Accuracy: Eliminates errors associated with using incorrect or outdated specifications.
- Simplified Information Management: The product manager can easily update and manage digital resources in one central location, automatically making them accessible via the QR codes.
- Cost Reduction: Reduces the need for printing and distributing physical documentation.
- Enhanced Safety: Ensures local partners have immediate access to critical work safety guidelines, minimizing potential accidents.
- Scalability: Easily scalable to accommodate new products, updates, and a growing number of global partners.
- Multilingual Support (Optional): The system can be configured to provide information in the local language of the user, further enhancing usability.
Summary
By using a Keycode Asset Management system with mobilecodes for sharing product information, the company empowers its global partners with instant access to critical digital resources. This leads to increased efficiency, improved accuracy, enhanced safety, and streamlined information management, ultimately contributing to smoother global operations and stronger partner relationships.